By Axel Boilesen, February 2013
Chris Boilesen, my Dad, had
many talents as builder and inventor. On our farm where I
was born and grew up near Cotesfield, Nebraska, the barn and
his blacksmith shop were areas that saw alot of activity and
many successful projects.
The Farm's Blacksmith Shop
I doubt if the shop area was
more than 16 feet by 16 feet but it contained a forge, a hand-cranked
post drill, a large workbench, a large anvil, vice, tool chest,
stock of angle iron and pipes of various diameters and lengths
and many other raw materials that he salvaged and collected
over the years into small junk piles adjacent to the blacksmith
shop. My Dad knew the resources he had to work with and I
believe he had plans in his mind well in advance to starting
each project based on what he had to work with and how it
would all come together.
I admired his creativity. And
the amazing thing was that it was all in his mind without
any preliminary drawings.
Water System
An early example of his creativity
was the water system he created for our home and for the livestock
on our farm. We had a tall windmill, probably 50 feet high,
with a forced pressure cylinder. The windmill was approximately
50 feet from the house. The layout of the water system was
as follows:
A new galvanized pipe was installed
from the windmill to the pantry (well below frost depth) and
that pipe was connected to a cubical storage tank about 3'
by 3' by 3' which was mounted in the ceiling of the pantry.
As part of the system when the kitchen tank was full, an overflow
pipe would discharge the excess water back outside to a horse
tank with a similar overflow system that took the water into
a cystern with piping to the hog yard and additional valves
to the cattle feed lot.
This water, pipe and temporary
storage system provided fresh cold water to the kitchen and
washroom year-round. We did not have electricity on the farm
until many years later but continuous fresh drinking water
was quite a treat. The system was fully automatic and relatively
maintenance free.
Ensilage System
Another system that I'll always
remember my Dad for was the system in the barn that he developed
for feeding ensilage to the milk cows. I'm guessing the size
of the pit silo for storing the fodder was about 15 feet in
diameter and 25 feet deep. The pit silo was adjacent to the
north end of the barn and had a shed type roof. Ensilage was
stored in this pit and the ensilage cutter to produce the
fodder was a production it itself using an old Republican
truck with a belt and pulley system as the power source. The
silo had adequate capacity to last most of the winter.
This takes me to the ensilage
system itself. Once the silo was filled the fodder needed
to get to the cows. It was this system for bringing the ensilage
through the opening in the barn and depositing it at the head
of the milk cows that I still marvel at.
The system consisted of steel
cable, pulleys, much angle iron to serve as trackage, a steel
box about 4' by 4' by 4', and more angle irons and pulleys
to connect the large carrier box to the lifting device. The
process was to lower the box unit into the pit silo, fill
the box and lift the filled unit of ensilage with a winch
assembly made up of pulleys, cables, steel drum, and a large
2 foot long crank to give added leverage. Added features were
included to control the pulley on the box for access to the
angle iron track. My Dad had the unique ability to visualize
the added features to make it work. And by creating such a
system it saved all of us alot of work, eliminating the need
to carry by ensilage by hand.
Gutter System
A mechanical system that again
took advantage of our farm's blacksmith shop and scrap iron
was the sytem my Dad constructed to clean the gutters built
into the floor just to the rear of the cows. The hauling device
was like a half barrel with linkage to a track. The cart part
was commercial and my Dad's part was building the track and
cable system to transport the loaded units with a tripping
device to empty the contents over a manure pile 50 feet beyond
the back of the barn.
Modified Disc Machine
I've always thought this farm
implement modification that my Dad made was worthy of obtaining
a patent as its function was to store rainwater as well as
allowing minimum tillage which is so popular even up to today's
farming methods. In case you weren't raised on a farm, a disc
or disc harrow is a farm implement that cultivates the soil.
You disc before you plant but it can also be used to weed
and after the crops have been harvested to chop up what is
remaining from the plants.
In the 1920's we had a disc
that was pulled by a team of 2 horses and even when I was
old enough in the 1930's to work in the fields we still used
horses to disc our fields where we were trying to grow corn
and hay. Discing wasn't always a good thing and I can remember
what seemed like many endless hours going back and forth across
that land and discing those dry hills that had hardly seen
a drop of rain the whole season and wondering what was the
point. Looking back at those Great Depression years in general
discing probably did contribute to the Dust Bowl when no rain
and no crops could not prevent the soil from being blown away
by the wind. But each year we would start the cycle again
and hope for rain and hope for things to get better. So in
that context my Dad's spirit of inventiveness was partly survival,
partly hope but certainly noteworthy for his creativity and
resourcefulness.
My Dad's modification started
with a standard disc approximately 12 feet in size. The standard
disc was round and shaped like a dish or saucer. The outside
diameter was approximately 18 inches with a square hole for
the shaft approximately 1 1/2 inches in size. The square shaft
kept the large discs all rotating as a unit with spacers between
each 18 inch disc spread at least 9 inches apart.
His modification was to cut-out
a pie shaped wedge of approximately 1/4 the projected area
of the disc leaving each disc as approximately 3/4 the original
circle. The notched out discs were then reassembled on the
square shaft, each one being a quarter circle ahead of the
previous cut-out disc.
The performance was exceptional.
We called it the waffle disc because when the field work was
completed the field surface looked like one huge waffle.
What could be better to prevent
excess runoff and soil erosion? Of course rain was essential
for farming and for this modified disc to really have a chance
to fully demonstrate its advantages we had to survive the
drought of the 1930's during which time we did lose our farm.
But even after we lost our farm we moved a few miles away
and were farming again the next year.
Eighty years later I have still
not seen anything quite like it. Simple vision of making a
good thing better and all in just a crude blacksmith shop.
A sad part of this story is
that I never took the time to tell my Dad that he had a good
mind and mechanical vision that his family can always be proud
of.
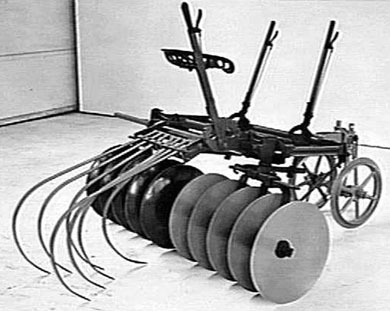
A somewhat smaller
version of the disc machine modified by my Dad.
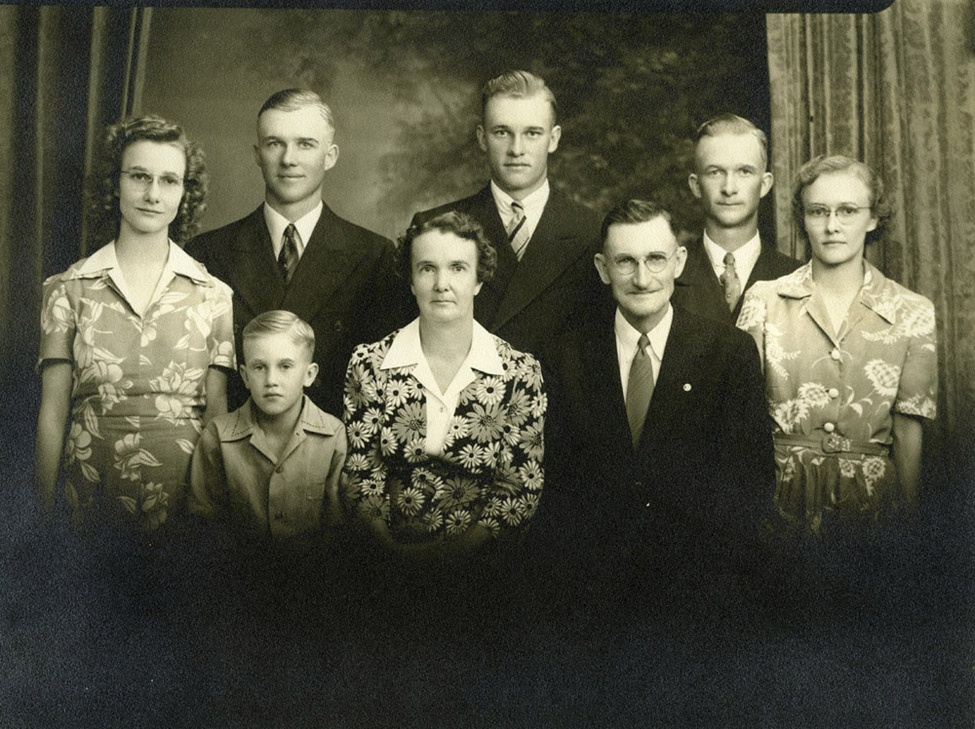
Chris and Elizabeth Boilesen
family portrait, approximately 1943, Cotesfield, NE; Back
row left to right Fern, Floyd, Axel, Lester; Front row left
to right Garold, Parents Elizabeth and Chris Boilesen, Lois.
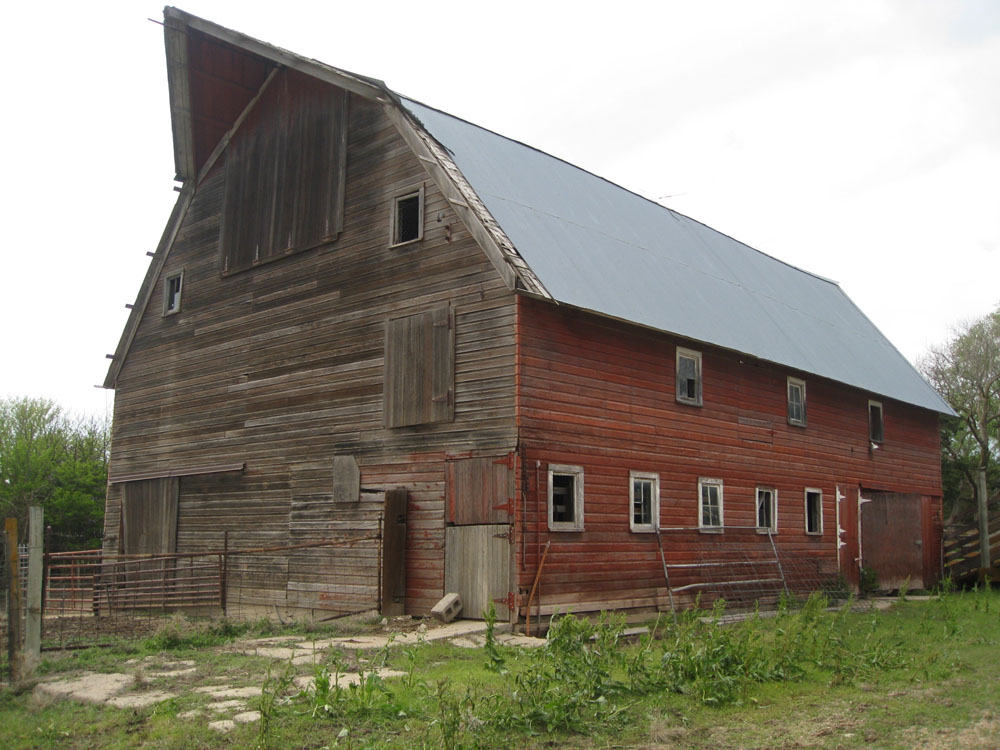
The original Chris Boilesen
homestead barn as seen in 2013 approximately 100 years after
it was built. The house and blacksmith shop are no longer
standing nor are the other 'systems' that were developed in
the 1920's and 30's by Chris.
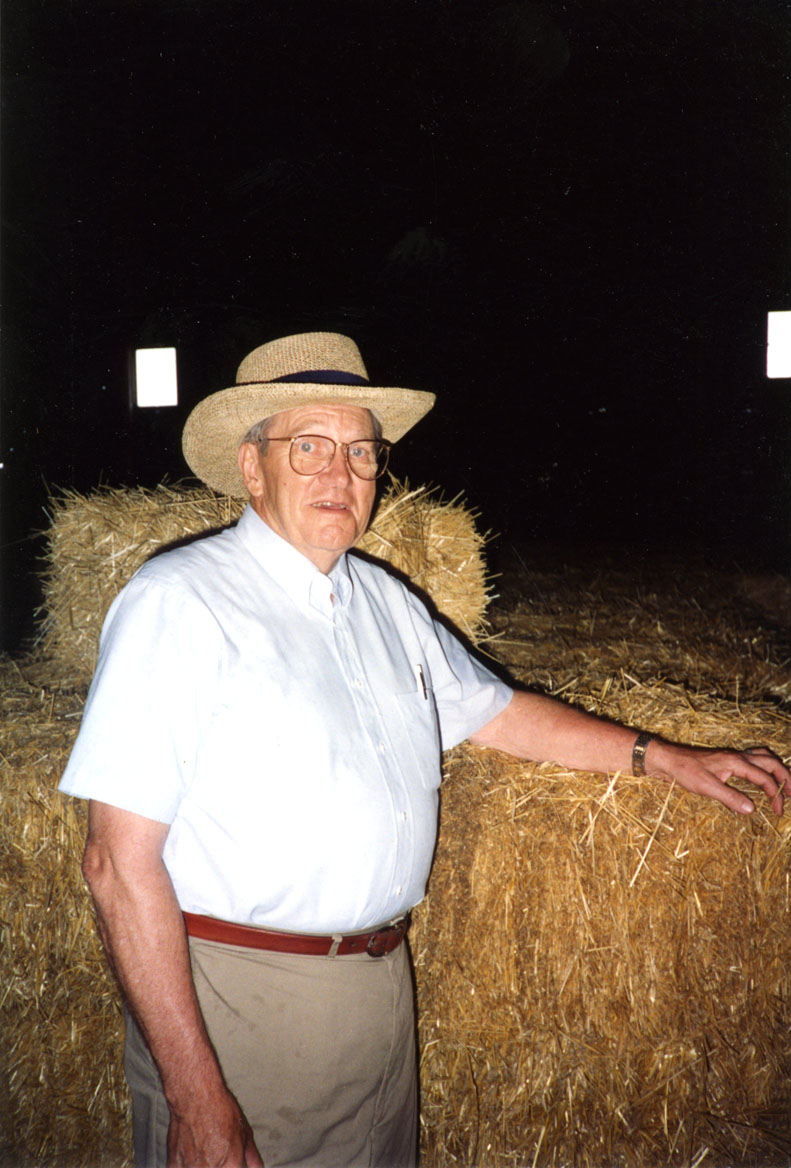
Axel visiting
original barn circa 1988